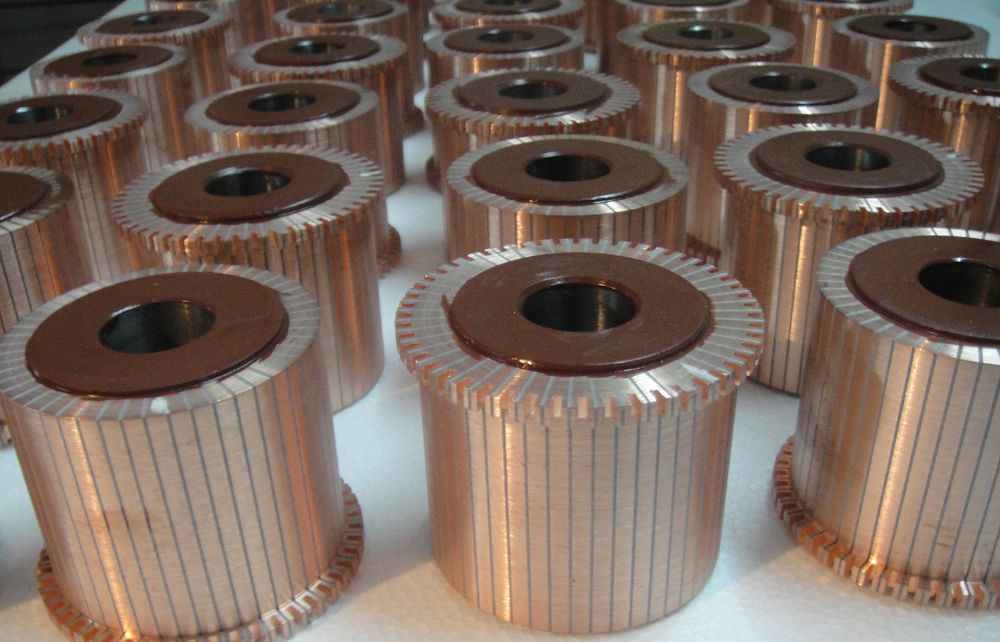
Molded Commutators
Molded Commutator manufacturing involves following stages
Raw Matrial:
- Hard Drawn electrolytic (99.9%;purity) or Silver Bearing Copper (0.1% Silver) is used. Silver bearing copper offer better heat resistance and bearing properties (Low wear of carbon brushes even at relatively higher temperatures.)
- Separator Mica - For "H" Class insulation Alkyd Vinyl Bonded Mica & for "F" Class insulation Shellac Bonded Mica is recommended. We use Alkyd Vinyl Bonded Mica (finely ground resin bonded).
- Commutator molding material - Thermoset glass-reinforced DMC based on unsaturated polyester resin, this molding material possesses superior mechanical strengths, temperature resistance beyond 250°C, very high electrical insulating strengths, especially arc & track resistance and is fire retardant.
Process:
- Copper lengths (normally multiple of segment length) received in trapezoidal form are cut to Segment Length (Segment length is Brush Length + Riser Width) with machining allowance.
- Segment is punched into 'L' shaped & 'V' grooves (with machining allowance for plain & profile turning). Separator Mica is punched as per Copper segment with additional length for Mica Projection on Riser side.
- Punched Copper Segments & mica segments are held secured in specially designed collet fixture. Assembly is retained in position by insulated steel rings at both ends.
- Commutator is molded by heat gelation process in specially design hydraulic press / fixture.
- Molded Commutator is then machined and tested as per customer's specifications.
Quality & Testing:
- Dimensional check using precision measuring instruments.
- Spin test - Commutator is checked for segment / bar rise on diameter in spin test.
- Hipot Test - Segment to Segment and Segment to Earth Hipot test.
- Insulation Resistance - Megger Test for Insulation Resistance.